Here is a photo of the nascar style bar.

The bar in the center is more or less the same thing as our tortion bars. How can I use the stock tortion bars to make a sway bar?
First of all, take the old tubes, cut off the splined ends. These are going to be the ends of my trailing arm linkages. The other end of the linkages, will be a spherical bearing mounted inside of a tube. I will then link the two pieces with a 3/16" piece of sheet steel.
Now take two tortion bars, cutting off one splined end of each. Machine the cut ends to a taper to accept weld. Weld the two bars together. Now machine the weld flat. I plan on welding a tube over top of the joint for added strength.
To mount it to the axle, I plan on using pillow blocks, which will mount to the axle via welded brackets.
The spherical end of the linkage will be mounted via bracket. This bracket will mount over the old frame rail, and will be welded on.
You can see below my idea. It shouldnt cost me much more than 50 dollars, and will be 100% custom and one of a kind. I can also change spring rates with different tortion bars.
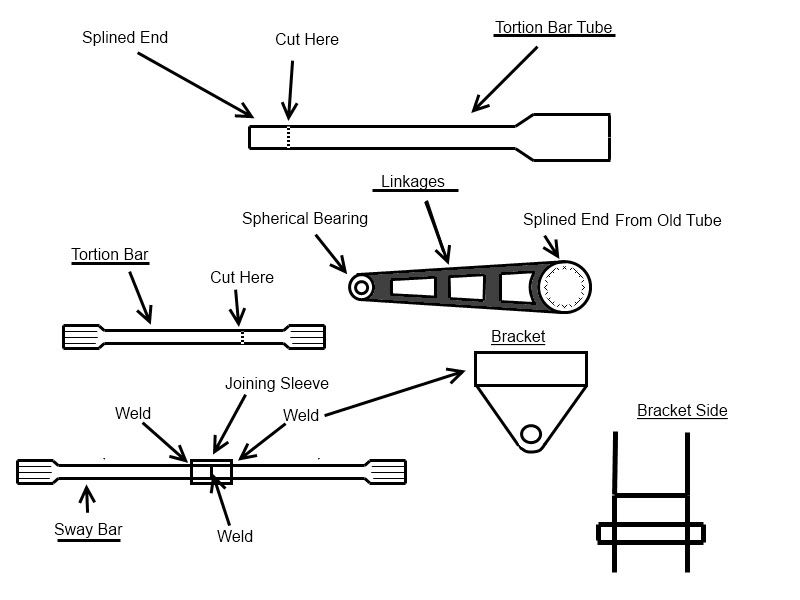